The cassava bags manufacturing process is a remarkable journey from nature’s renewable resources to a sustainable alternative to traditional plastic products. These eco-friendly products are making waves as they address the concerns of plastic pollution and environmental sustainability.
From the cassava fields to your hands, this eco-friendly journey transforms natural resources into non-toxic, biodegradable, and renewable packaging solutions. Here we will dig deeper into the process.

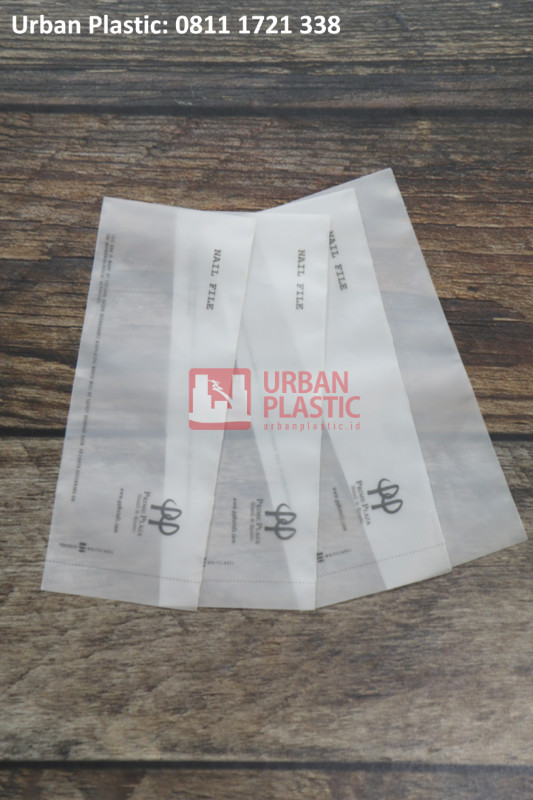
Cassava Bags Manufacturing Process
We will delve into the fascinating manufacturing steps. Get ready to know the steps that transform cassava starch into an eco-conscious packaging solution.
1. Cultivating Cassava
The journey begins in the fields, where this hearty and drought-resistant root vegetable is cultivated. Cassava is grown predominantly in tropical regions and requires minimal water and agricultural inputs, making it a sustainable and abundant source of raw material for the product.
2. Harvesting and Processing
Once the plants mature, they are harvested, and the roots are carefully extracted. In the Cassava bags manufacturing process, these roots are then cleaned and processed to obtain the starch. The roots are peeled, grated, and subjected to a step that separates the starch from the fibrous components.
3. Starch Extraction
The extracted starch is a key ingredient in the manufacturing of the product. This starch is a natural, non-toxic, and renewable resource, making the product an eco-friendly choice. The starch undergoes a meticulous refining method to ensure its purity and quality.
4. Mixing and Formulation
The starch is then combined with other eco-friendly ingredients, such as water, natural plasticizers, and UV protectants, to create a dough-like mixture. In the Cassava bags manufacturing process, this mixture is crucial for the bag’s strength, flexibility, and durability.
5. Extrusion and Shaping
The formulated cassava-based mixture is extruded to create sheets of material. These sheets can be of varying thickness and are then shaped into the desired bag sizes. The sheets are cut and moulded to create bag-like structures.
6. Drying and Curing
The newly formed items are dried and cured to remove excess moisture and ensure their strength and resilience. This step helps in preventing the item from deteriorating while in storage or use.
7. Quality Control and Testing
Before being distributed for sale, in the Cassava bags manufacturing process, the product undergoes rigorous quality control and testing. This includes checks for strength, flexibility, and biodegradability, ensuring they meet stringent eco-friendly standards.
8. Customization and Printing
The product can be customized to meet specific requirements. Whether you need a branded item for your business or special designs for personal use, the product can be tailored to your preferences. This customization step involves printing and design applications.
9. Packaging and Distribution
Once the items pass quality checks and are customized to your specifications, they are carefully packaged and distributed to local and global markets. This step ensures the availability of the product to consumers looking for sustainable and eco-friendly packaging solutions.
As more consumers and businesses opt for this product, they contribute to reducing plastic pollution and protecting the environment for future generations. Cassava bags manufacturing process has proven that this is not just an eco-friendly product, but contributes to a greener future.
For more information about Cassava bags please contact: Whatsapp/Mobile Phone: +62 811 1721 338 (Ms. Ais) or Email : info@urbanplastic.id.